Purge gas or purge. Molecular seal is an unfortunate name given to a flow restriction installed in a flare stack to minimize the amount of purge gas required.
Pdf Purge Reduction Device A Guide To The Selection Of Gas Seal In A Flare System Semantic Scholar
Optionally there may also be an alternative gas recovery system in place.
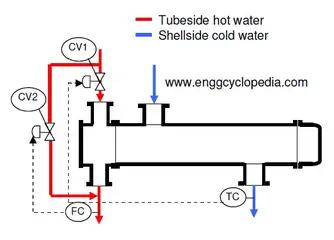
. 2-10 28 Determination of Combustion Efficiency Representing Good Flare. On the other hand a water seal drum uses the same way except that the sealing fluid is water and the drum is instaled at the flare stack base after the knock-out drum vessel whereas moleculare seal is instaled at the top of flare stack before the tip. The seal is normally flanged between the flare tip and stack and is designed to prevent air from entering the flare system.
Buoyancy seals use a couple of concentric baffled cylinders in the path of the purge gas as indicated in figure-1. The flare vendor will have to provide details on design options and required. Figure 1 shows an image of an onshore elevated flare stack where the knock-out drum seal drum flare stack molecular seal and flare tip are all visible.
Further information on typical flare system design can be found in ISO 23251 2006. Velocity purge seal mounted in base of flare tip and uses the velocity of the purge gas through the seal to sweep any atmospheric air in the flare tip. 2-6 25 Flare Test Methods.
Buoyancy seal typically uses the difference in densities of the purge gas and ambient air to keep the air from entering flare system. Molecular seals cause flow reversal. 2-7 26 Combining All Available Test Run Data.
The gas molecular seal is installed in the flare stack near the flare tip. The Argo AMS is a standard labyrinth type used throughout the flare industry and can be used with purge gases lighter or heavier than air. The molecular type seal forces the purge gas to make two U turns forming a seal because of the different molecular weights.
Molecular seals require a continuous stream of purge gas but the amount of purge gas is less than would be required without the seal. The overflow line from the water seal at the flare stack base included an emergency shutoff valve that would automatically close if the level of water in the. DESIGN FEATURES Molecular seal can maintain an effective seal for up to 8 hours after loss of purge gas supply Velocity seal provided with weep holes to allow drainage Molecular seal complete with drain connection inspection port Both seals provide significant savings in operating costs Extends flare tip life by minimizing burn back No moving parts.
DuhonGATE Chemical 27 Jun 08 1751. The location of NAOs seal design reduces purge gas reduction but and extends. Molecular seal reduces purge gas requirement by 98.
Figure 1 - Schematic of a buoyancy seal in a flare stack indicating purge gas path. Light gas is trapped at the top of the U-tube. The molecular seal included a drain line with a U-seal and isolation valve at the bottom.
As indicated in figure-1 liquid seal at the flare stack base is essentially a cylindrical volume of liquid into which the gas inlet to flare stack is dipped. Purge flow is required to prevent air ingress into the flare stack. They also protect gas processing equipment from becoming overpressured by releasing excess non-waste gas via.
Liquid seals at base of flare stack. Molecular seal creates a labyrinth to more efficiently sweep any atmospheric air in the flare tip. Two types of seals are commonly used.
A molecular seal also could be very efficient in reducing the amount of purge gas required to maintain a positive. Velocity seal reduces purge gas requirement by 94. The other is a liquid seal containing a mixture of glycol and water which has a relatively low freezing point.
NAOs Fluidic Flare with Multi Baffle Fluidic Seal and Solid Conical WindFlame Shield provides for minimal purge gas flow while maintaining maximum safety reliability and protection for the equipment. 24 Air Injection Rates and Tip Design for Available Flare Test Data. In the water seal liquid tank design combined with practical engineering experience it provided application.
What is Molecular seal in flare system. These are generally used in flare systems for gas plants and others where freezing is an issue for seal pots and mol sieves. NAO was the first to introduce the Multi Baffle Velocity Type Purge Gas reduction seal in 1972.
Also known as flare stacks flare tips molecular seals are elevated vertical conveyances found in oil gas wells rigs refineries chemical natural gas plants and landfills. They are used to eliminate waste gas that cannot be otherwise used or transported. The seal is a gas inversion device causing the gas normally flowing in an upward direction to be turned.
Flare System Design for Oil and Gas Installations Flare Seal Drum Primary Duty To prevent flashback from flare tip back to flare headers To avoid air ingress into flare system during sudden temperature changes and to maintain positive system pressure Design Specifications Water as liquid sealing fluid not recommended for extremely. Gas to avoid air ingress into the system. This paper briefly introduces the main process of flare system elaborated with emphasis the water seal liquid tank design.
AFS MOLECULAR SEALS The Molecular Seal AFS Series is located just below the flare tip and has been designed to prevent air ingress to the flare riser thus preventing the formation of an explosive mixture in the system. An improved molecular seal for installation in a flare stack system designed for burning of waste gases of lesser density than air and for installation at an intermediate point in the flare stack comprising a housing of larger cross-section than that of the flare stack the housing being closed by plates at both ends with an outlet conduit. Flow is required to prevent.
Effective purge gas includes. One is a gas seal called a molecular seal. Molecular seals depend on the density difference between air and hydrocarbon gas.
This volume allows the flow of flared gas from inlet pipe to. Gas seal is a device used in flare systems which uses purge. Install seals in the flare stack and immediately upstream of the flare stack.
The purpose is to minimize flare gas purge rates which would otherwise be large and create velocity conditions at the tip that will minimize tip flame impingement and damage of the flare tips. In the energy and petrochemical industry the use of the flare to burning VOCs is a conventional approach for port energy storage tanks. 2-9 27 Data Removed After Being Considered.
The molecular seal included a drain line with a U-seal and isolation valve at the bottom. The difference in purge gas and air densities sees the purge gas form a molecular barrier in either the top or in the bottom. They normally are located below the flare tip and serve to prevent air entry into the stack.
The overflow line from the water seal at the flare stack base included an emer- gency shutoff valve that would automatically close if the level of water in the base was too low.
Buoyancy Seal And Velocity Seal For Flare Stack Enggcyclopedia
Flare System Part Flare Process Flare Drums Flare Seals The Piping Talk
Buoyancy Seal And Velocity Seal For Flare Stack Enggcyclopedia
Manage Change To Flare Systems Aiche
Purge Reduction Seals Velocity And Molecular Seals Encore Combustion
Manage Change To Flare Systems Aiche
Buoyancy Seal And Velocity Seal For Flare Stack Enggcyclopedia
0 comments
Post a Comment